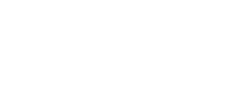
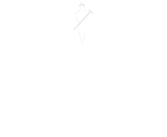
The benefits of one integrated system for your service and maintenance work
To keep all communication and information flows clear and manageable, it is recommended to opt for one integrated software solution where all processes come together and data flows across the system. Thus, you can organise all information, from the receipt of service notifications to the sending of the invoice, in one system. This means you only have to enter all information once, saving time and reducing the administrative burden.
Many construction and maintenance businesses still use disconnected solutions for service and maintenance processes. However, decentralised data has many drawbacks. In order to really ensure good cooperation with your supply chain partners, it is important that you exchange real-time information with them quickly and efficiently. Furthermore, you must make sure that your systems are in sync. Working with different tools that do not or only partially communicate with each other is not efficient. You can have certain processes functioning well, but if the other processes in your business do not connect with them, they will not work effectively altogether. In short, one integrated software system in which all service and maintenance processes are incorporated is of great importance. In this blog, we explain why an end-to-end software system would be incredibly beneficial for your service and maintenance process.
1. An overview = one version of the truth
To keep all communication and information flows clear and manageable, it is recommended to opt for one integrated software solution where all processes come together and data flows across the system. Thus, you can organise all information, from the receipt of service notifications to the sending of the invoice, in one system. This means you only have to enter all information once, saving time and reducing the administrative burden.
2. Optimisation of the service and maintenance process
By using an integrated software solution you have real-time insight into your business processes. Errors often arise when information is not up-to-date and when decisions are made based on incorrect data. For example, if something changes in the schedule, this will affect the field service engineer who has been allocated to the job. Real-time data allows you to make immediate decisions and adjustments when necessary. This means you can always send the best suited field engineer to the right location with the right materials.
3. Speak the same language as your supply chain partners
Speaking the same language is the basis of a successful collaboration. That is why it is important that everyone in the supply chain collaboration, works from the same source. This means that everyone has access to the same up-to-date and accurate information. By using an integrated communication Portal connected to your ERP system, you can share information with each other in real time. There are software solutions such as 4PS Construct, which can be linked to the tools or solutions used by supply chain partners. This allows your supply chain partners, for example, to make a notification in the communication platform and you will receive this notification directly in your ERP system. So, everyone works in the same system and there is a single source of the truth.
Curious about which digital tools and communication platforms you can use in the service and maintenance process? Read our whitepaper: ’10 steps how to digitise your service and maintenance processes in construction’.
-
Share:
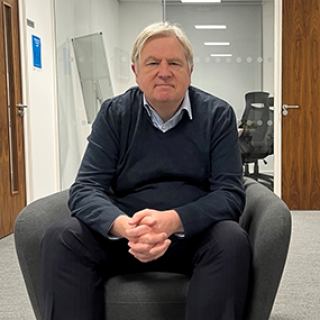
About the author
Elliot Herdman | Elliot has over 20 years experience in the construction industry working with main contractors, subcontractors, M&E, supply and install analysing their business processes and implementing digital software solutions to improve projects, drive efficiencies and meet the growing needs of clients.